JACKING ROBOTS – Laser SLAM Lifting Robot AMB-300JZ
Main Category
AGV AMR / jack up lifting AGV AMR / AGV automatic guided vehicle / AMR autonomous mobile robot / AGV AMR car for industrial material handling / China manufacturer AGV robot / warehouse AMR / AMR jack up lifting laser SLAM navigation / AGV AMR mobile robot / AGV AMR chassis laser SLAM navigation / intelligent logistic robot
Application
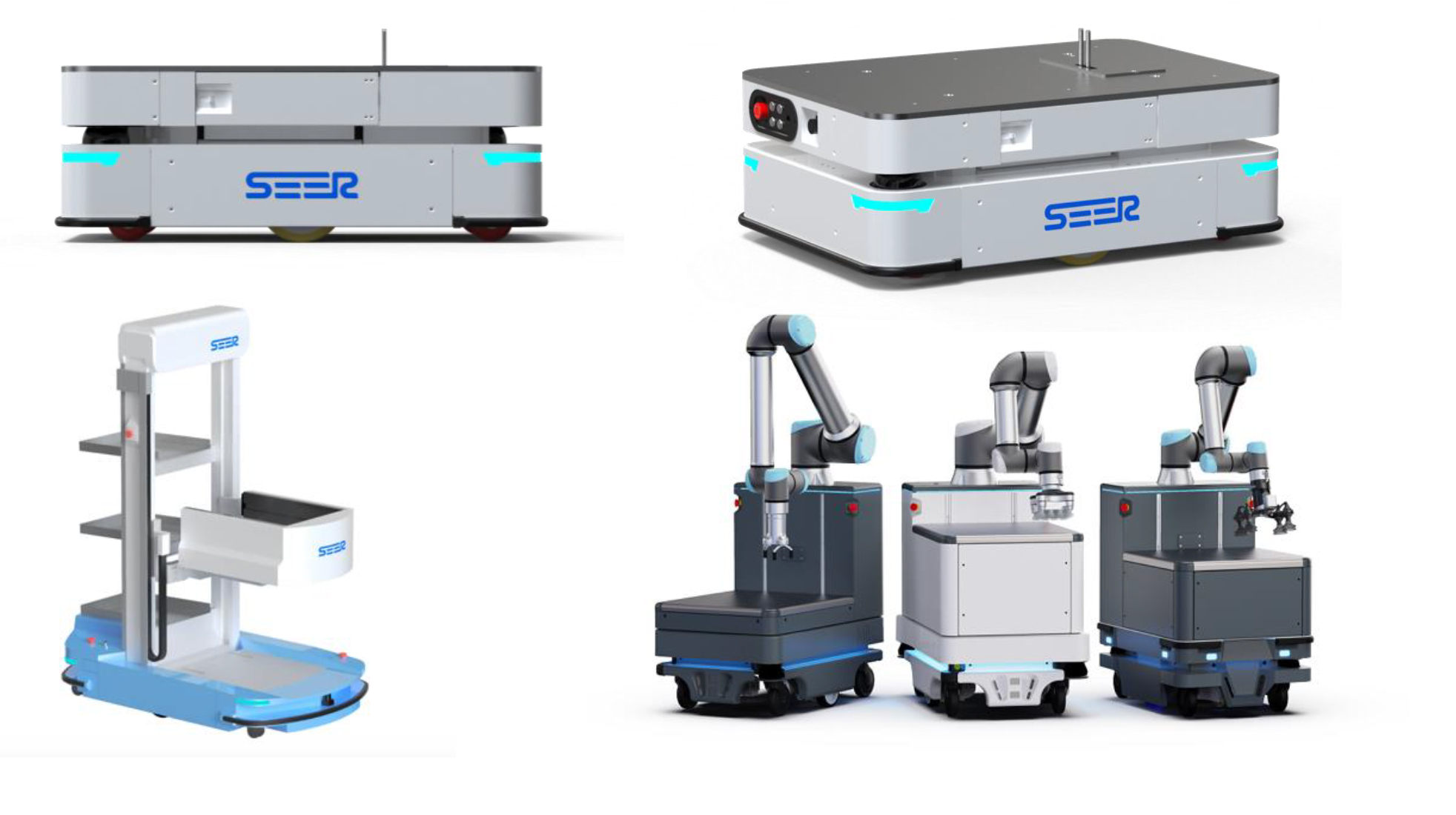
AMB Series Unmanned Chassis AMB (Auto Mobile Base) for agv autonomous vehicle, a universal chassis designed for agv autonomous guided vehicles, provides some features such as map editing and localization navigation. This unmanned chassis for agv cart provides abundant extent interfaces such as I/O and CAN to mount various upper modules together with powerful client software and dispatching systems to help users quickly complete manufacture and application of agv autonomous vehicles. There are four mounting holes on the top of the AMB series unmanned chassis for agv autonomous guided vehicles, which supports arbitrary expansion with jacking, rollers, manipulators, latent traction, display, etc. to achieve multiple applications of one chassis. AMB together with SEER Enterprise Enhanced Digitalization can realize the unified dispatching and deployment of hundreds of AMB products at the same time, which greatly improves the intelligent level of internal logistics and transportation in the factory.
Feature
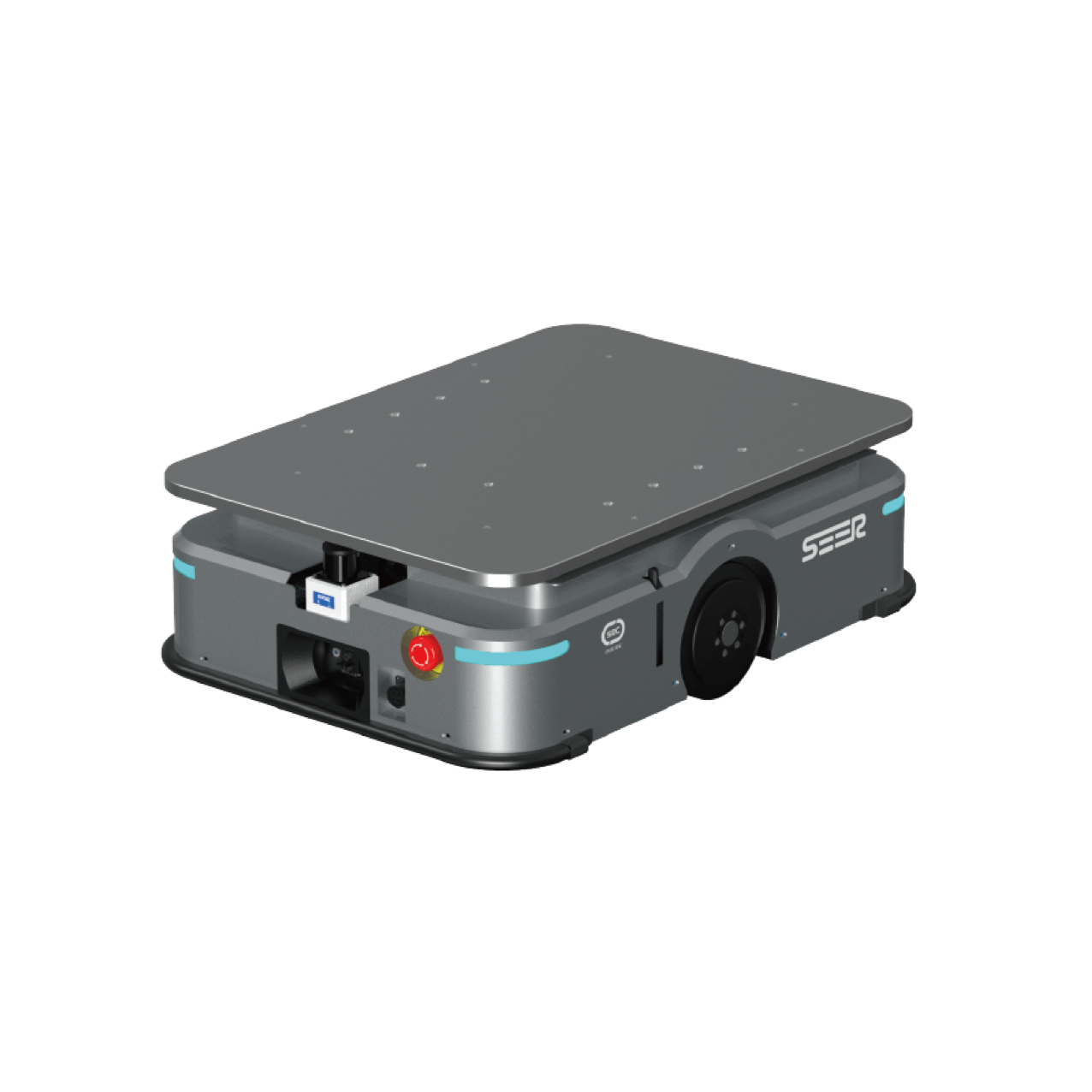
· Rated Load: 300kg
· Run Time: 8h
· Lidar Number: 2
· Rotation Diameter: 910mm
· Navigation Speed: ≤1.5m/s
· Positioning Accuracy: ±5,0.5mm
● More Powerful Algorithms
Shelf identification and correction, high dynamic environment position and navigation, slip detection and correction, QR code secondary precise positioning, hybrid navigation, automatic following, and using fifth-order Bézier curve.
● Powerful Material Shelf Identification
A variety of goods racks can be identified and it can moveunder the racks and jack the goods. it can also identify material racks in various industries.
● Smaller and More Flexible
The smaller size allows for a lower chassis height with the integrated climbing mechanism, lower environmental requirements, more coverage scenarios, and less site restrictions.
● More Secure and Efficient
Dual lasers and bumper strip sensors at the front and back for 360° protection; 10minutes of charging for 1 hour of running.
● New Industrial Design
With SEER Robotics' new design PI language, present customers with a powerful and high-tech product of metal texture.
Related Products
Specification Parameter
Product name | AMB-300JZ | AMB-JS | AMB-800K | |
asicparameters | Navigation method | Laser SLAM | Laser SLAM | Laser SLAM |
Drive mode | Two-wheel diffe rential | Two-wheel diffe rential | Two-wheel diffe rential | |
Shell color | Cool Gray | Cool Gray | Black & gray | |
L*W*H(mm) | 792*580*250 | 1330*952*290 | 980*680*245 | |
Rotation diameter(mm) | 910 | 1460 | 980 | |
Weight (with battery)(kg) | 150 | 265 | 150 | |
Load capacity(kg) | 300 | 500/1000 | 800 | |
Jacking platform dimensions(mm) | 760*545 | 1300*920 | φ640 | |
Maximum jacking height(mm) | 60±2 | 60±1 | 60±2 | |
Performance parameters | Minimum passable width(mm) | 640 | 1050 | 820 |
Navigation position accuracy(mm)* | ±5 | ±5 | ±5 | |
Navigation angle accuracy(°)* | ±0.5 | ±1 | ±0.5 | |
Navigation speed(m/s) | ≤1.5 | ≤1.5 | ≤1.8 | |
Batteryparameters | Battery specifications(V/Ah) | 48/20(Lithium Iron Phosphate) | 48/40(Lithium Iron Phosphate) | 48/27 (Lithium Iron Phosphate) |
Comprehensive battery life(h) | 8 | 7 | 8 | |
Automatic charging parameters(V/A) | 54.6/15 | 54.6/40 | 54.5/15 | |
Charging time (10-80%)(h) | ≤1 | ≤2 | ≤2 | |
Charging method | Manual/Automatic | Manual/Automatic | Manual/Automatic | |
Configurations | Lidar number |
2(SICK nanoScan3+FREE C2)or 2(FREE H1+FREE C2) |
2(SICK nanoScan3) |
1(SICK nanoScan3 Core)or 1(OLEILR-1BS5H) |
Number of low-position obstacleavoidance photoelectric | 0 | - | 0 | |
Cargo detection | - | 〇 | - | |
E-stop button | ● | ● | ● | |
Speaker | ● | ● | ● | |
Atmosphere light | ● | ● | ● | |
Bumperstrip | ● | ● | ● | |
Functions | Wi-Fi roaming | ● | ● | ● |
Automatic charging | ● | ● | ● | |
Shelf recognition | ● | ● | ● | |
Spin | - | - | ● | |
Precise location with QR code | 〇 | - | 〇 | |
QR code navigation | 〇 | - | 〇 | |
Laser reflector navigation | 〇 | 〇 | 〇 | |
Certifications | EMC/ESD | - | ● | - |
UN38.3 | - | ● | ● |
* Navigation accuracy usually refers to the repeatability accuracy that a robot navigates to the station.
● Standard 〇 Optional None
Our Business
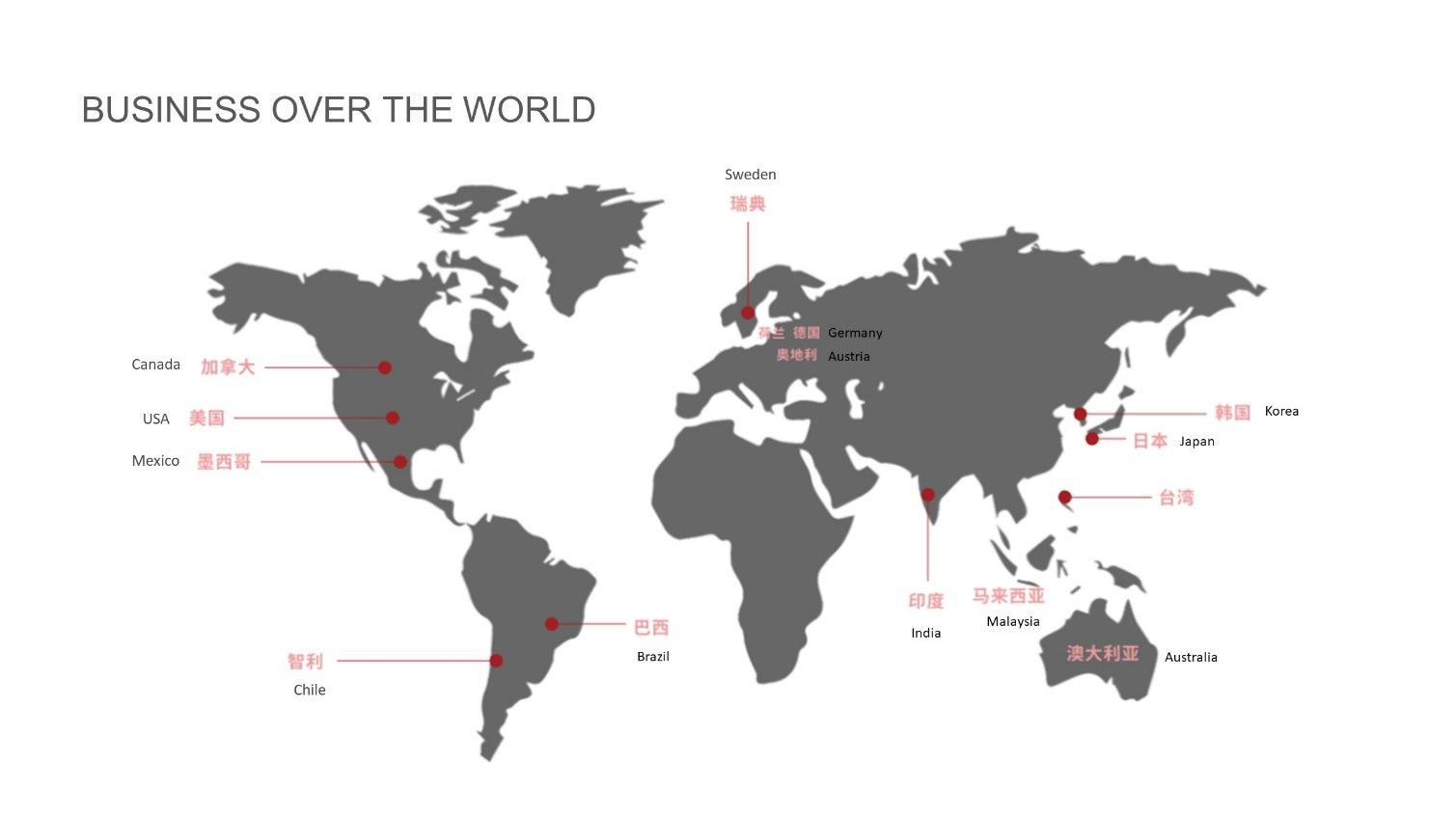
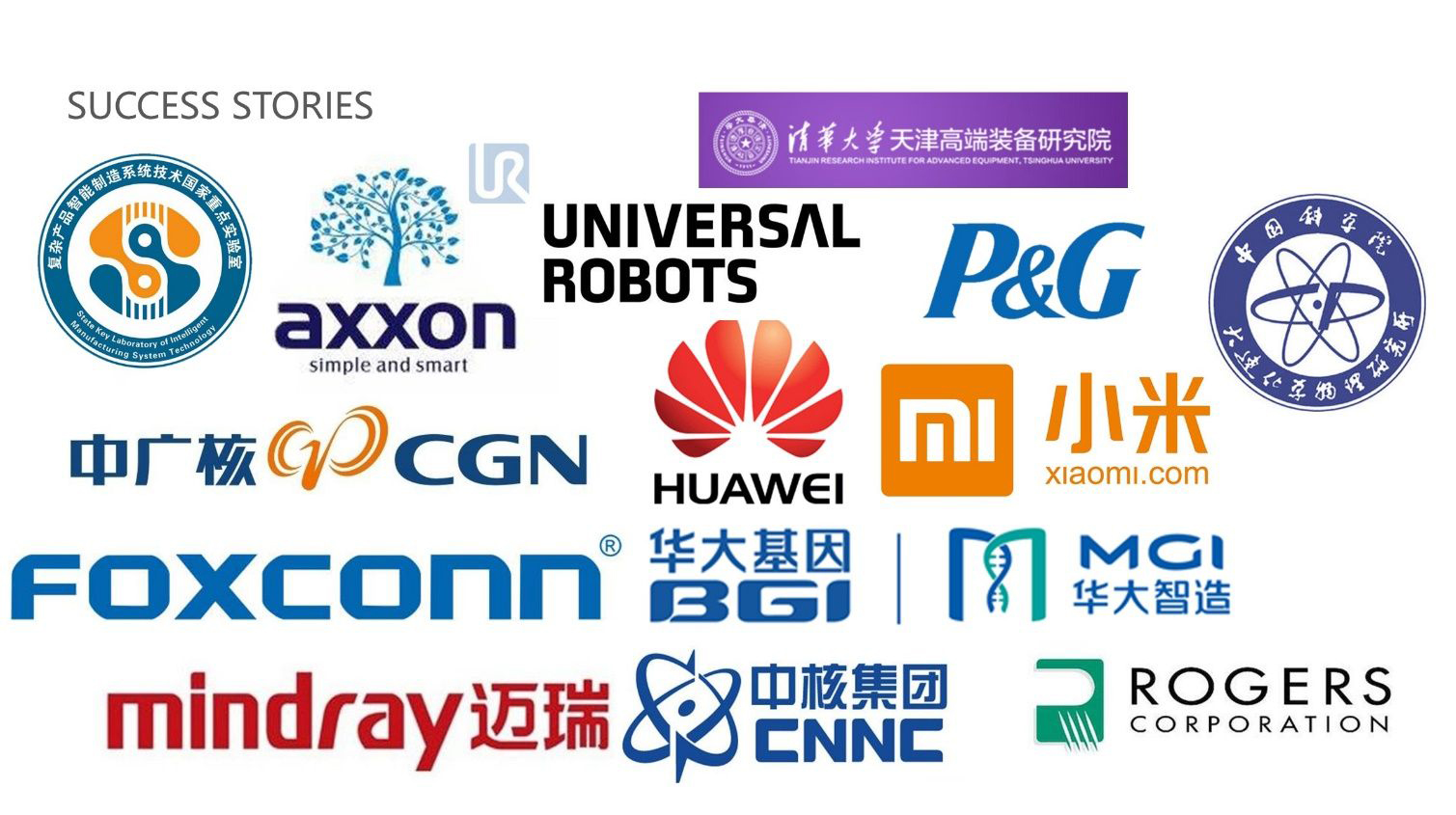